The electrical generation sector is facing a future of disruptive changes with the implementation of more renewable energy, a higher demand of electricity due to more electric transport and newly developed storage technology.
Power plant digita…
WE BRING YOU TECNATOM MONITORING CENTER :
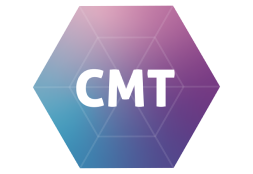
Remote Monitoring Services for Energy Plants
ON-LINE FLEET/PLANT STATUS
PLANT PERFORMANCE & ASSET CONDITION
ALERTS ON POOR PERFORMANCE, FAILURE RISK AND DIAGNOSIS
REPORTS
TECHNICAL SUPPORT
DATA FLOW: FROM FIELD SIGNAL TO MONITORING SERVICES
DATA INGESTION
DATA SECURE
DATA INTEGRATION
PROCESSING AND ANALYSIS
VISUALIZATION
ONLINE DASHBOARDS
MOBILE AND EMAIL ALERTS
REPORTING
HISTORIAN GRAPHICATION
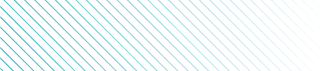
Benefits
EXPERTS FOCUSED ON COSTUMERS
– Experts in operations, performance, maintenance, processes, and engineering.
– Using the cutting-edge TecOS Suite tools.
DATA ANALYSIS
– Data analysis applied for early detection, diagnosis, and prediction of anomalies.
– Our team of data scientists tackles the analysis of complex problems, combining process knowledge with advanced algorithms.
ADVANCED INTERFACES
– Application of human factor engineering geared towards minimizing human error, reducing cognitive load, and improving ergonomics.
– Smart icons developed by Tecnatom to present, in a visual and comprehensive way, the most representative parameters.
ADAPTABLE AND FLEXIBLE
– Functional scope that is flexible and adaptable to our clients’ needs and requirements.
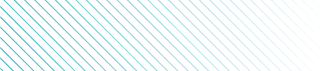
Tecnatom Monitoring Center features
Reduction of operation and maintenance costs.
- Optimization of O&M costs thanks to the reduction of fuel consumption, the reduction of equipment failures, and the implementation of predictive maintenance.
- Economic approach by identifying and monetizing the impact of losses.
Early detection of anomalies.
- Data analysis aimed at reducing equipment failures.
- High-performance interfaces that facilitate early identification of events.
- Real-time data access.
Supporting decision making.
- Analysis, diagnosis, and recommendations based on criteria from expert analysts from different fields.
- Identification of best practices and lessons learned.
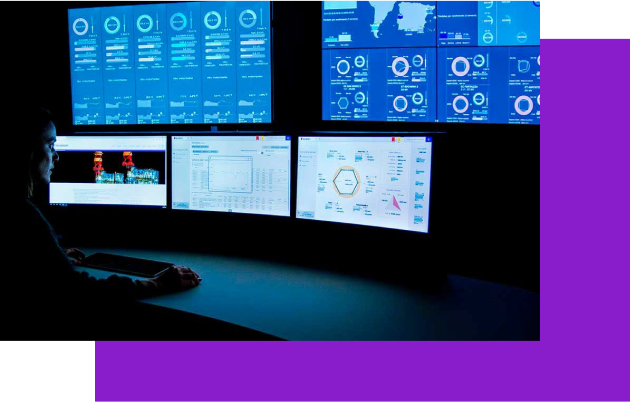
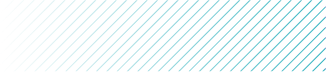
What can you do?
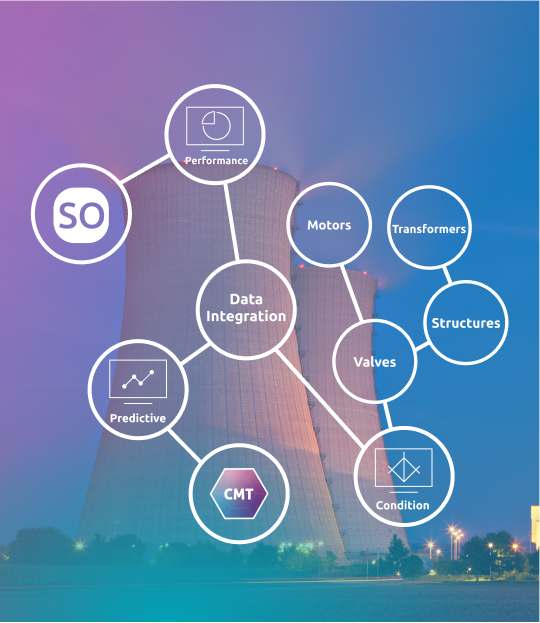
Plant operations and maintenance strategies can be optimized thanks to real-time knowledge on equipment efficiency and condition. Scope:
- Monitor performance with TecOS SOLCEP
- Foresee degradation and emerging equipment problems with TecOS FORESEE.
- Monitor the state of components like valves, transformers, motors, and structures.
Our expert analysts rely on these tools and on their process knowledge to report events, to make recommendations, and to offer personalized advice.
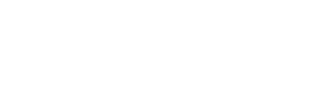
How does it work?
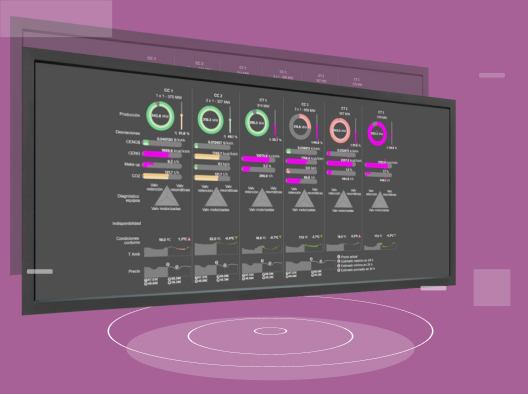
Tecnatom Monitoring Center aims to support energy plants to optimize operation and maintenance. The data and the TecOS Suite solutions provide support for our monitoring and diagnosis services.
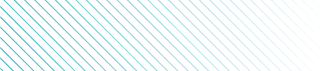
Inside the CMT
The team
The CMT team uses different profiles from analysts and experts who work collaboratively with plants. The center’s staff is supported by their knowledge on the technologies, processes, and tools to be able to make the most of the available data. Our relationship with our clients is based on transparency. We design communication processes based upon our clients’ specific needs. In addition, CMT includes simulators that Tecnatom has developed and that allow to test different scenarios and give recommendations to our clients.
Interfaces
The information processed in the CMT is shown through smart interfaces that, thanks to pattern recognition and the integration of information, allow to identify anomalies at a glance. The use of smart icons, developed by Tecnatom, help to present information in a comprehensive, intuitive way,reducing the cognitive load on the user and favoring situational awareness. Tecnatom’s experience in human factor engineering has given rise to a design aimed at facilitating the work of analysts.
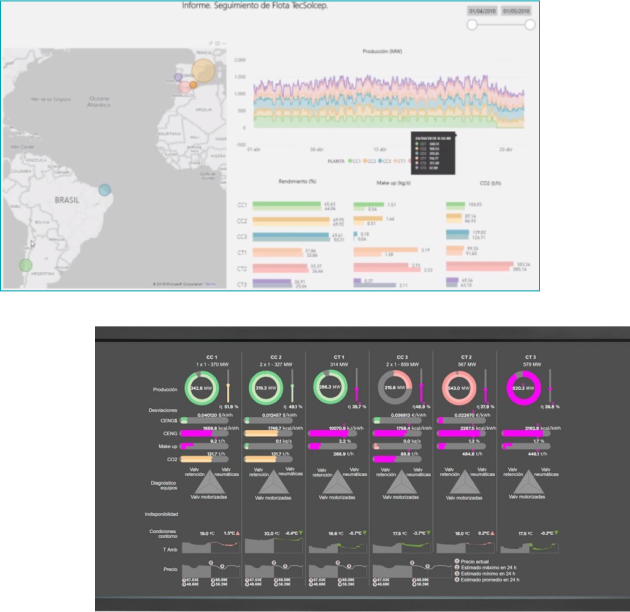
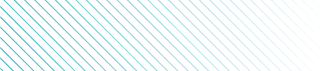
Services provided by the Monitoring Center
- Periodic reports
- On-Demand Services
- Communications and Accesibility
- Access to operating experience and best practices
- Operational reports.
- Reports focused on accounting.
- Reports with an executive profile.
- Diagnosis of inefficient situations.
- Analysis of instrumentation.
- Assessment of when it is appropriate to undertake certain maintenance.
Periodic reports.
- Operational reports.
- Reports focused on accounting.
- Reports with an executive profile.
On-demand services On-demand analysis and assessment to face unfamiliar situations. Diagnosis of in
- Diagnosis of inefficient situations.
- Analysis of instrumentation.
- Assessment of when it is appropriate to undertake certain maintenance.
Direct communication and accessibility to solutions and data.
- Communication between the center and our clients is based on fluidity and transparency.
- Remote access to all CMT solutions.
- CMT platform generates alerts for mobile devices and email.
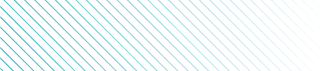
FAQs
Instrumentation analysis, process optimization recommendations, inefficient situation diagnosis, deviation impact analysis to support decision making.
Performance and component monitoring both require data sources and communications solutions. Storage takes place in a data management system. The best solution for deployment will be sought to meet the client’s needs
The architecture for acquisition, transport, and storage is flexible and adaptable to the client’s needs. CMT software has a wide variety of connectors to transmit and storage plant data in order to be able to take advantage of the data once it has been processed.
The communication process with plant staff is tailored to the needs of each client. Staff should be available for weekly and monthly follow-up, as well as being able to tend to alerts set off by monitoring system incidents.
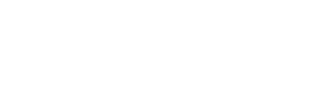
Blog News
Our world is changing at an unprecedented speed, involving challenges such as the population growth, the environmental degradation and the economic re…
The digital copy that enhances and improves the performance of the reality being replicated.
The term "digital twin" seems to be a magic concept in th…
The power generation industry is currently facing the need to reduce operating costs while maintaining the safety and availability of power plants. Co…